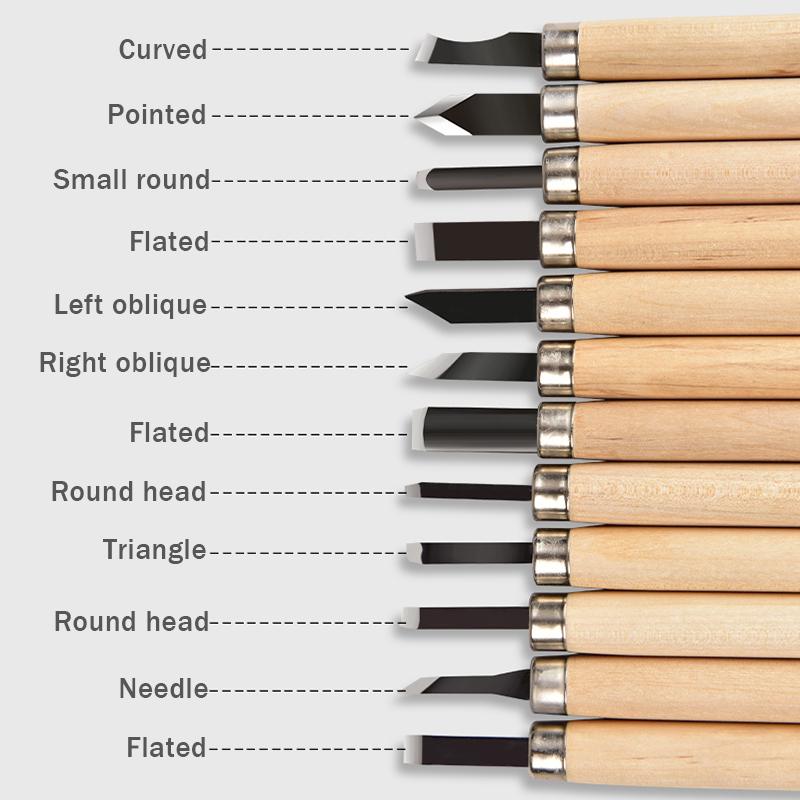
Before you start carving your walking stick, you will want to know which woods work best. You will also want to know about various techniques for whittling and what David Allen uses to carve his walking sticks. A few famous quotes about walking sticks are also available. These are some tips to help you create the perfect walking stick. Continue reading to find out more. Now you can carve a walking stick that will be a unique, functional piece of art!
Woods that work well for carving a walking stick
Finding a straight blank to carve is the most challenging part of the process. There may be a few branches that are too bent to be of use, but it is worth searching until you find one. The ideal time to harvest a straight branch is during the winter months when sap travels from branches to root, making the wood more stable and less likely to split. It's okay to harvest wood while the tree's still green if you cannot wait until spring.
For carving a walkingstick, you can choose from several species of wood. The North American hardwood Chestnut is strong. Because it is dense, it can be used to make walking sticks and other similar tools. This wood grain can be slightly or fully open depending on the species. It is a solid walking stick, which feels smooth and solid. It is also extremely attractive and is often used in carve. Some species can still be carved using the bark.
Techniques for cutting a walkingstick
You can use a few basic methods to carve your walking stick. First, pick a piece that has a unique texture. Some woods are unique in their bark colors and patterns, while others have natural swirls. You may want to enhance these features by using lacquer or paint. To make it more attractive, you can carve the wood shaft. Last but not least, make sure you pick a straight stick free of branches or sharp spikes.
This book will explain the differences between different types of wood as well as different carving styles. Snakes and lions are the most popular designs. You can carve realistic figures like fish, eagles and deer, in addition to snakes. Many people consider the skills of these artists to be God-given. This book can be used by both novice and advanced carvers.
David Allen uses these tools when carving a walkingstick
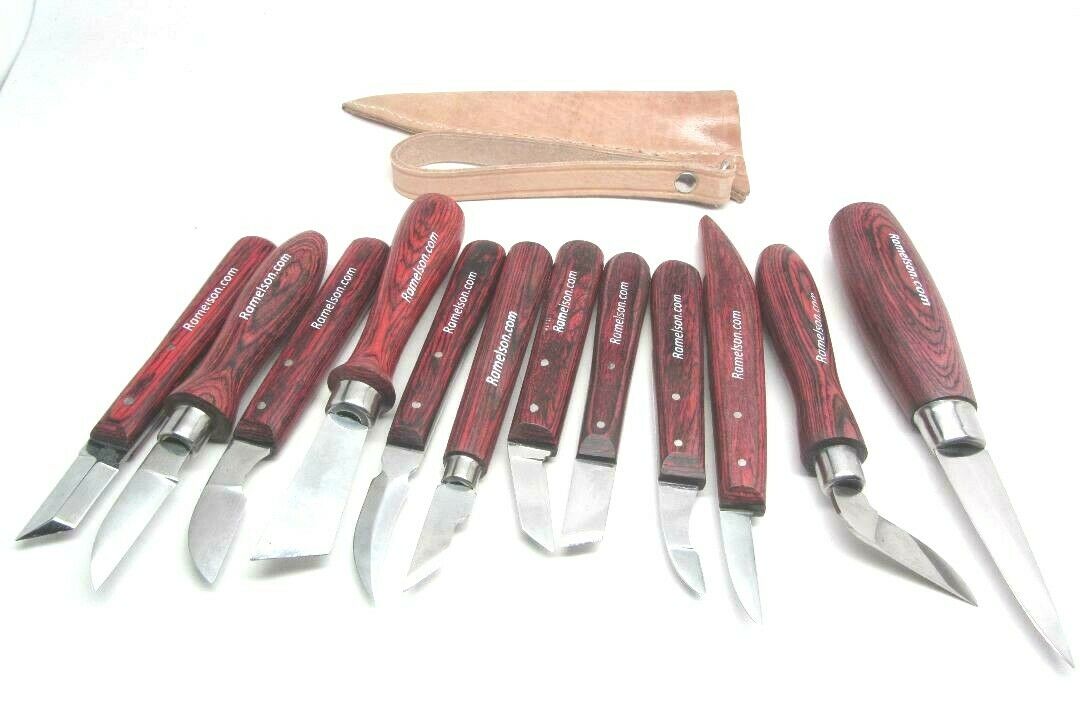
David Allen was just a small boy when he started to make toys with the pocketknife he had found under his house. Because he was too young to use a knife, he had to keep it secret from his family. His creations included toys like slingshots and utilitarian objects like shoeshine boxes. Allen began to carve walking sticks at the age of 15 after becoming disabled. Allen used a pocketknife as well as a chisel for carving the wood.
Allen developed his designs independently, digging around the roots of saplings and deciding on what to carve. He believed that a design needed to be "seemed" before it could carved. This was similar to the work of many African-American artists. Allen often had visions and dreams for the design he wanted. In this way, he was able to create a stick that would evoke the feelings and emotions of his community.
Famous quotes about carving a walkingstick
Carving a walkingstick is a complicated process and requires a blank. Straightening the blank is the most difficult part of the entire project. There are many options for where to get your stick. However, you need persistence to find the right one. Although it may look bent beyond practical utility, you can keep looking until you find one. You should try to cut your stick at the time sap flows from the tree's roots to its branches. The sap makes the wood softer and less likely that it will split.
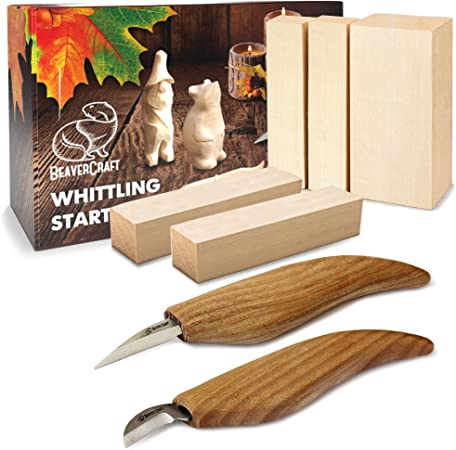
Consider the wood's color and texture when you are choosing wood. Every piece has a unique texture and color. There may be unique bark marks or swirls. A coat of lacquer will enhance these natural swirls. A smooth finish is possible by choosing a wood shaft that is free from branch shoots and tough spikes. This will make the process much easier. You should consider what type of finishing you will use, regardless of the material.
FAQ
Where can I start woodworking?
You can learn the most effective way to build furniture by actually building it. You will need tools. There are bound to be mistakes. But if your persistence is consistent, you will soon master the craft.
Choose a project that interests you. You could make something as simple or complex as a box. Or you could build a whole entertainment center. Once you've decided on a project, find a local woodworker who specializes in that kind of work. Ask them for their advice about the tools and where they can be found. Perhaps you could ask if there is someone else who does this type of work.
Can I make my living doing this job?
Yes! Many woodworkers are already doing so. According to the U.S. Bureau of Labor Statistics in May 2012, the median annual income for woodworkers was $34,000 This is more than the national average of 31,000 per annum.
What kind of wood should I use?
Woodworking is a popular job that involves oak, pine and maple. Each wood variety has distinct characteristics that influence the final product's look and feel. For example, oak tends to be darker and harder than other woods. Birch is light and soft, while mahogany can be heavier and more dense. You also have the option of solid wood or veneers. Veneers consist of thin sheets made from wood and glued together to form a single layer.
Statistics
- The best-paid 10 percent make $76,000, while the lowest-paid 10 percent make $34,000. (zippia.com)
- Woodworkers on the lower end of that spectrum, the bottom 10% to be exact, make roughly $24,000 a year, while the top 10% makes $108,000. (zippia.com)
- Overall employment of woodworkers is projected to grow 8 percent from 2020 to 2030, about as fast as the average for all occupations. (bls.gov)
- The U.S. Bureau of Labor Statistics (BLS) estimates that the number of jobs for woodworkers will decline by 4% between 2019 and 2029. (indeed.com)
External Links
How To
How to join hardwood without using nails
Woodworking is a popular hobby. Woodworking is a relaxing hobby that allows you to use your hands to create useful things from wood. However, there are times when you want to join two pieces of wood together without having to use nails. This article will show you how to do it to make your woodwork projects look great.
You will first need to trim the edges of your wood pieces before joining them. You don't want to leave sharp corners that could cause problems later on down the road. Now it's time to start glueing your boards together.
You should only glue one side of hardwood. For softwoods like cedar and pine, glue should be applied to both sides. Apply the glue to the boards and press them down until they are securely attached. After applying the glue, let dry the boards before proceeding to the next stage.
After you've glued your boards, you'll want to drill holes into the joints where you plan to insert screws. You can choose the type of screw to determine the size of your holes. For example, if your screw is a 1/2-inch wooden screw, drill a hole that is at minimum 3/4 inches deep.
Once you've drilled your holes, you'll want to drive the screws through the joint and into the backside of the board. Do not hit the boards' front surfaces. It will ruin the finish. Be careful not to drive the screws too hard at the ends. This will prevent splitting the wood's end grain.
Now that your project is finished, you'll want to protect it from the elements. You have two options: seal the whole furniture piece or just the top. You will want to choose a product that will be durable for many years. Some examples include oil-based varnishes, polyurethane, shellac, lacquer, etc.
You can find these products at most home improvement stores. It is important to ensure that you purchase the correct product for the job. Some finishes are toxic and should not ever be used indoors. So, always wear protective gear when handling them.