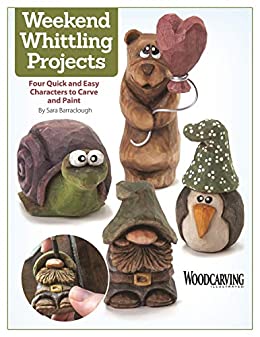
Chip carving begins with imagining where you want the blade to point. Start by cutting the tile at the point. Next, work your way upwards to create larger chips. You should not pry the chips out, but rather gently wiggle them. You can cut the tile a little deeper if bits are still attached to the tile. You will continue to do this until the tile appears finished. You can then create your own unique chip carvings using a pattern.
Freeform style carving
For free-form chip carving, you can use both a split and straight-edged cutter to carve a pattern on the wood. Split blanks allow you to use more power for carving because the fibers are straight. You can then cut in both directions by cutting flat the top layer of the wood and removing the bottom layer. You can improve your carving skills by using different templates.
It can be difficult to carve, but once you learn the basics, the rewards will be well worth it. The process of carving a design can be as tedious as the actual carve. Chip carving involves many cuts and ridges. It is important to ensure that the ridges are sharp at the bottom. The "sharpness of the ridges, regardless of whether you are carving a circle or not, is crucial.
Using angled cuts
If you are using an angled knife for carving a chip, it is important to visualize how the cut will look. The chip will probably have two sides. One of the sides will be straight. Generally speaking, the cut will be made with the point of the knife positioned at the intersection of the two straight walls. Then, you will want to make a third side cut, which should meet the two previous side cuts at the deepest point.
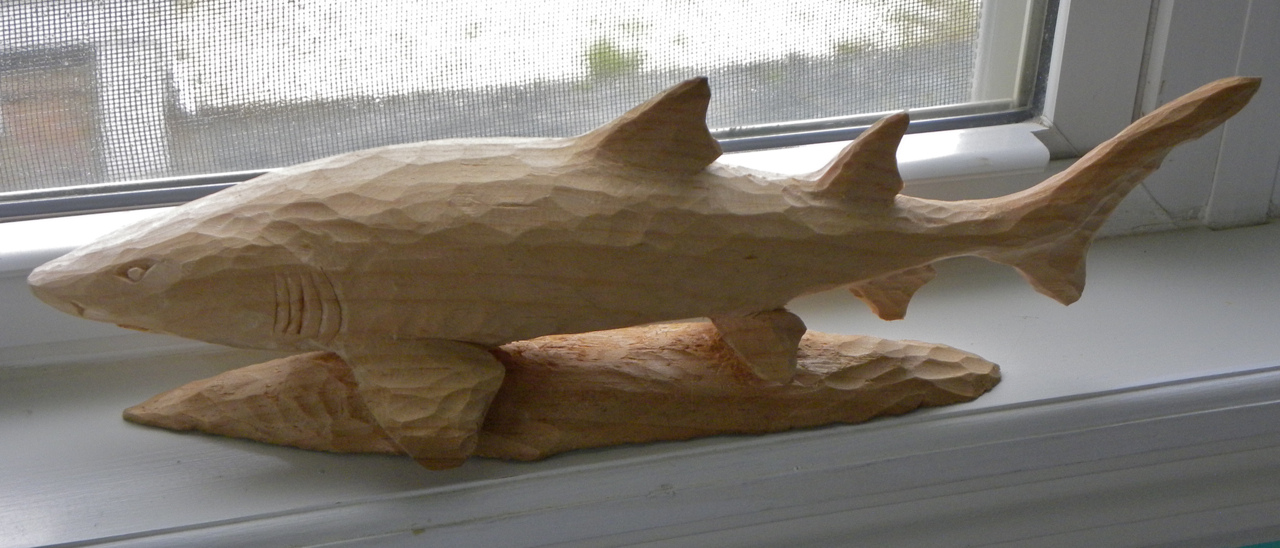
Chip carving works best with lighter wood. This creates a stronger contrast between the negative and positive spaces. A lighter wood color will allow for greater contrast in shadows. Straight chips will highlight the negative space above them, while angled chips will create a subtle shadow that will appeal to the eye. It will appear as if the letters are being removed from the wood if the chip is angled.
Flexcut knives:
A Flexcut knife is a great choice if you are looking to start chip carving. These American-made knives feature a sharpened edge and are pre-sharpened. They should be stropped regularly with Flexcut Gold polishing compound. The ideal bevel angle for this knife is 15 degrees. For chip carving, you should hold the knife at this angle.
The Flexcut knives can be a great tool for chip carving if you're not a pro at it. Every Flexcut knife has a reliable, long-lasting edge. The handles are made of ergonomically-shaped wood. These knives provide precise control over each cut and reduce the chance of chipping. Flexcut offers a special coating which prevents chipping to protect your carving tools.
A pattern is made
First, draw a design to create a chip-carving pattern. The pattern can be either free-form or it can have basic geometric shapes such as squares, circles, and ovals. It is essential to keep the lines straight. It may take a few tries, but it will eventually become second nature. By making a practice piece of scrap wood, you can learn the pattern. Once you have a design, you can start carving.
You can draw a grid to help you carve squares. You can experiment with different patterns and create unique pieces. A ruler and pencil are required to draw the pattern. Each cell must be square, and each side should be between 3/16" and 1/4". To create triangles from the corners of the cells, you can connect them to each other.
Getting started
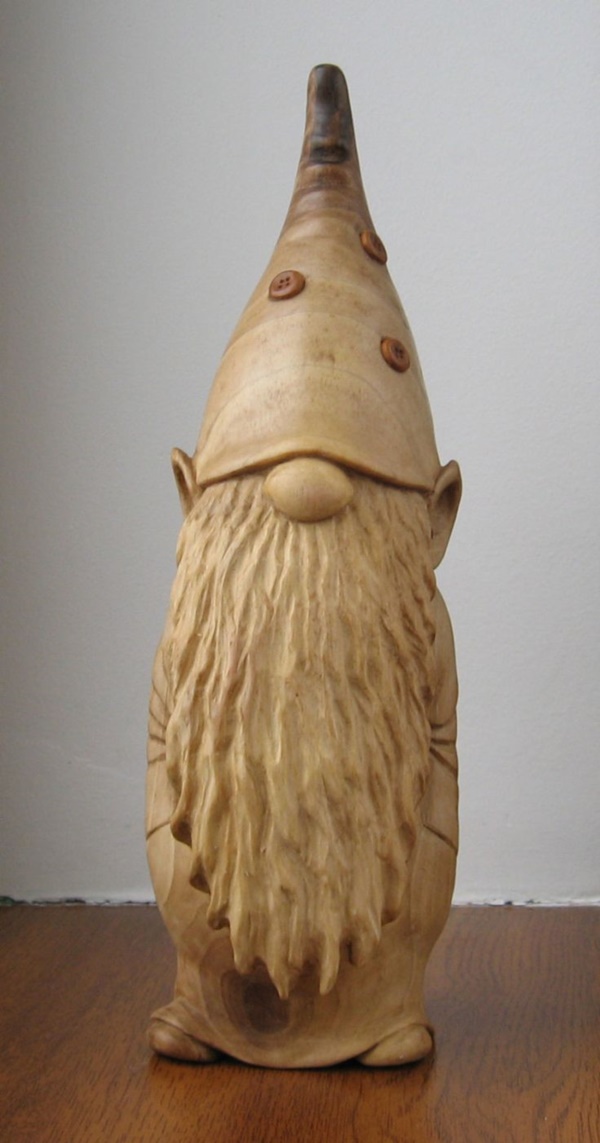
Learn the basics of chip carving before you start. You can trace a pattern on the wood with graphite, which is a common design. You can use a ruler to ensure accuracy as you trace along the edge of the wood. To erase traced lines, you could also use a pencil or eraser. After you have perfected this technique, practice on a larger work surface until you get a firm grip.
One of the best things about chip carving is that it is incredibly easy to learn and doesn't cost much. Compared to other wood carving techniques, chip carving is easy to master. Chip carving is a great way to express your creativity and create beautiful pieces. Chip carving can be used to create personal pieces that you can give as gifts or for your own use. It's a rewarding hobby that can easily be passed down to the next generation. To get started, you can practice your chip carving skills on a small piece wood such as a wooden spoon.
FAQ
Are there any other things I should know regarding woodworking?
It is easy to underestimate how much work it takes to make furniture. Finding the right kind of wood is the most difficult part. It can be hard to choose from the many types of wood that are available.
Another problem is that not all wood has uniform properties. Some woods will warp and others will split or crack. These are important considerations to make before you purchase wood.
How long does it take to finish a piece of furniture?
It depends on the wood type you choose, the complexity and the amount you apply to the finished product. For example, hardwoods require more maintenance than softwoods. Hardwoods also tend to be more expensive than softwoods. But they last longer, and resist moisture better. Finishing furniture can take anywhere from one week up to three months.
Where can I find free woodworking plan?
For free woodworking blueprints, you don’t need to read any magazines or buy any books. Just search Google. Search Google for "free woodworking" to see hundreds of sites that provide free plans.
How can I keep my shop organized?
A designated place to store your tools is the first step towards keeping your workshop clean. To keep your tools sharp and ready for work, keep them clean of dust and debris. Pegboard hooks can be used to hang tools and accessories.
How can you calculate woodworking pricing?
Remember to keep costs as low as you can when calculating project costs. It is important to ensure that you are getting the best materials prices. It is important to take into consideration all factors that can impact the cost of your projects. These include time, skill and experience. If you want to get an idea of what you can expect to spend on different types of woodwork projects, check out our guide to the average price of common household DIY tasks.
How much should a hobbyist invest to get started?
If you're looking to start your own woodworking business, you'll probably need some capital to buy the necessary tools and supplies. A good place to start would be by buying a small table saw, drill press, circular saw, jigsaw, and sanding machine. These items won't break the budget and aren't expensive.
Where can I buy woodworking supplies?
There are many places that you can find all the information you need. You could shop at your local hardware store or go online to Amazon.com.
You can also check garage sales and flea markets for old furniture and other materials you can reuse.
Statistics
- Overall employment of woodworkers is projected to grow 8 percent from 2020 to 2030, about as fast as the average for all occupations. (bls.gov)
- Most woodworkers agree that lumber moisture needs to be under 10% for building furniture. (woodandshop.com)
- Average lumber prices rose about 600 percent between April 2020 and May 2021. (familyhandyman.com)
- In 2014, there were just over 237,000 jobs for all woodworkers, with other wood product manufacturing employing 23 percent; wood kitchen cabinets and countertop manufacturing employing 21 percent. (theartcareerproject.com)
External Links
How To
How to make wood joints
This tutorial will show how to join 2 pieces of wood together. The "pocket hole joint" is a method whereby we drill holes into the wood and glue them together. This works well if the wood is straight and smooth. If your wood isn't straight or flat, you might want to try another method, such as dowel joinery. Here are the steps
-
Drill Pocket Hole Joints. To start, measure and mark where you want to put the pocket hole joint. You will then drill 3/4" deep holes through each piece of wood with a jigsaw, handheld drilling machine, or hand-held drill.
-
Sand Smooth. Sanding the edges of the wood will help to prevent the joint from splitting later.
-
Glue both sides together. Apply glue to both ends of the wood. Allow the wood to rest for five minutes before clamping it together.
-
Connect the pieces. After the glue has dried you can attach the pieces to form a flush joint.
-
Trim Joinery. Trim any excess wood surrounding the joint once the glue has dried completely.
To be able to turn the pieces inside-out, leave enough room between them.